Glycol cooling systems operate on the principle of heat exchange. They utilize a mixture of water and food-grade propylene glycol to efficiently regulate and maintain the temperatures of various stages in the brewing process. The glycol mixture, chilled by a refrigeration unit, is circulated through a closed-loop system of pipes and heat exchangers, transferring heat away from the target areas and maintaining precise temperature control.
In a 5000L beer brewery equipment, the glycol cooling system plays a critical role in maintaining the desired temperature during both the mashing process and fermentation. During mashing, the glycol system helps control the temperature of the water used to activate enzymes and convert starches into fermentable sugars. In fermentation, the glycol system assists in controlling the temperature of the fermenting wort, which is crucial for yeast activity and the development of flavors.
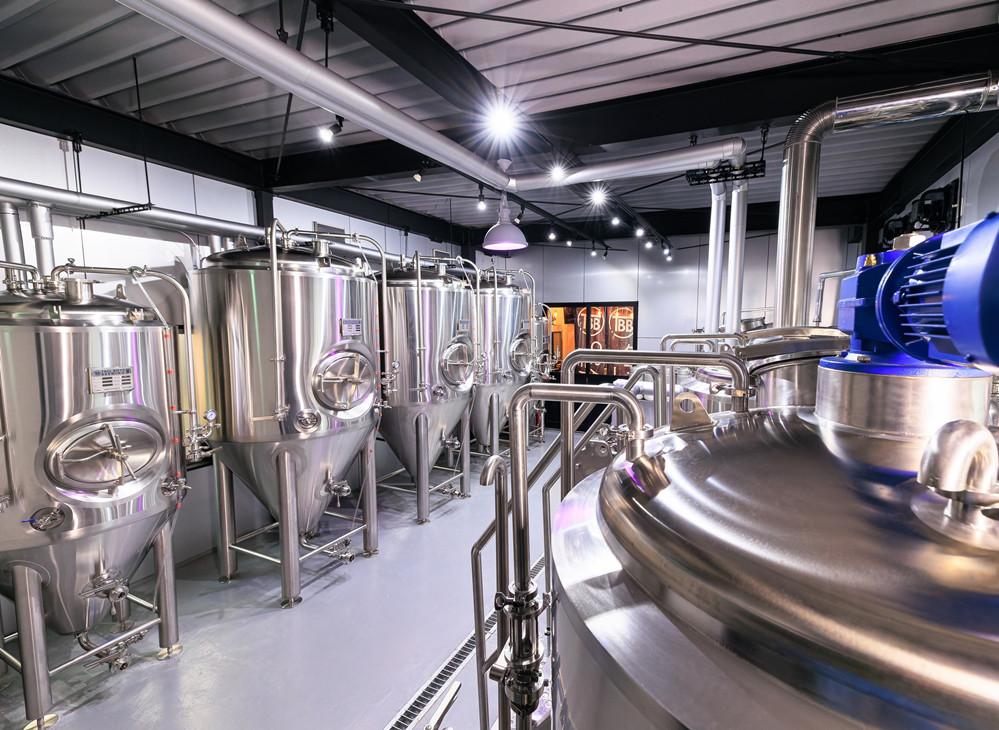
Benefits of Glycol Cooling in a 5000L Brewery:
Temperature Precision: Large-scale brewing requires precise temperature control to achieve consistent results. The glycol cooling system allows brewers to fine-tune the temperatures within fractions of a degree, ensuring that each batch maintains the desired characteristics.
Yeast Management: Yeast health and activity are influenced by temperature fluctuations. A glycol cooling system provides the optimal environment for yeast to thrive, resulting in efficient fermentation and the creation of distinct flavors and aromas.
Reduced Risk of Contamination: Closed-loop glycol systems minimize the risk of contamination by preventing the introduction of outside air, ensuring a hygienic environment for the brewing process.
Time Efficiency: Rapid temperature changes are achievable with glycol cooling systems, allowing brewers to transition seamlessly between different phases of brewing without prolonged waiting times.
Consistency in Quality: With precise temperature control, the glycol cooling system contributes to the consistent quality of the final product. This is particularly important for breweries aiming to establish a reliable brand identity and loyal customer base.
Energy Efficiency: Glycol cooling systems are designed for efficiency, using less energy to maintain temperatures compared to other methods. This is a crucial consideration for breweries concerned about their environmental impact and operational costs.
Maintenance and Considerations:
While glycol cooling systems offer a range of benefits, they also require proper maintenance to ensure their continued functionality. Regular monitoring, cleaning, and servicing of the system components, including pumps, heat exchangers, and refrigeration units, are essential to prevent breakdowns and maintain performance.
Breweries opting for a glycol cooling system should also consider factors such as glycol mixture ratios, system size, and capacity to ensure the system meets their specific brewing equipment requirements.
Contact Information:
Email: [email protected]
Contact Person: Emily Gong
Get In Touch