Tiantai Company, based in Jinan, China, is a leading manufacturer of beer and beverage equipment. With expertise in designing and providing turnkey solutions, Tiantai includes tubular heat exchangers in its comprehensive lineup of equipment, tailored to breweries worldwide.
This article delves into the significance of tubular heat exchangers in beer brewing, explaining their functions, differences from plate heat exchangers, and the principles of designing capacity for brewing applications.
What is a Tubular Heat Exchanger?
A tubular heat exchanger is a type of heat transfer device that uses a series of tubes to exchange heat between two fluids. One fluid flows through the tubes, while the other flows around them within a shell. Heat is transferred across the tube walls, efficiently exchanging thermal energy.Key features of tubular heat exchangers include:
· Robust Construction: Typically made of stainless steel for corrosion resistance and longevity.
· Simple Design: Consists of a tube bundle enclosed in a shell.
· Flexibility: Can handle a wide range of fluids and operating conditions.
Tubular heat exchangers are widely used in industries requiring high levels of hygiene, such as food and beverage production, making them an excellent choice for breweries.
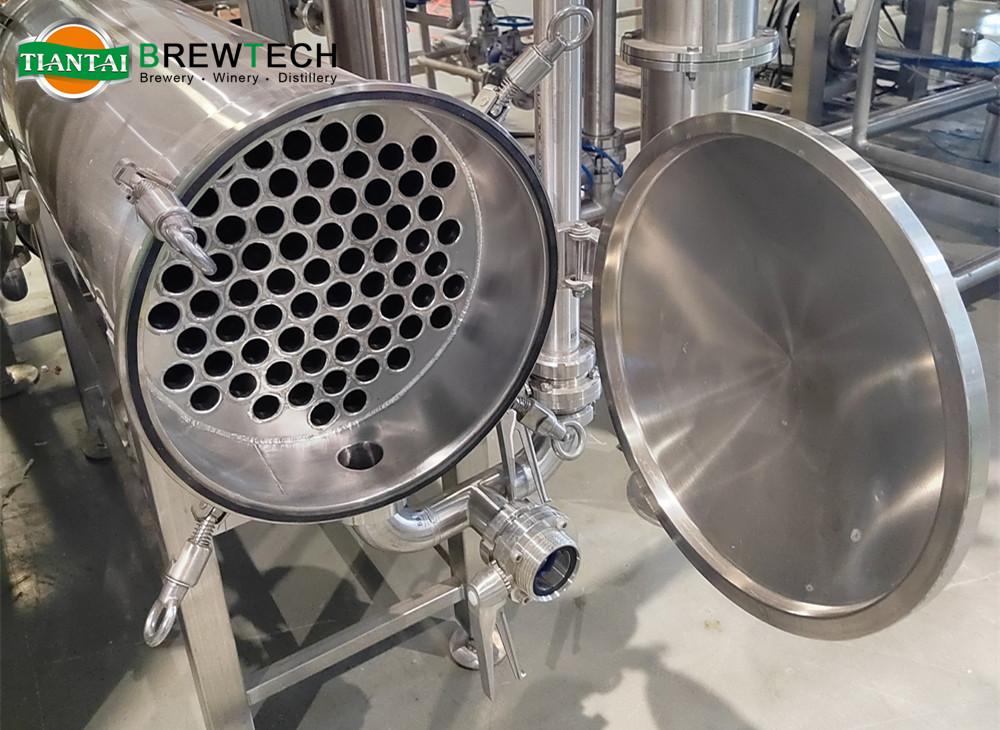
What is the Function of a Tubular Heat Exchanger in Beer Brewing?
In beer brewing, tubular heat exchangers are used for precise temperature control and efficient energy management during key processes, including:1. Wort Cooling
After boiling, the hot wort must be rapidly cooled to a specific temperature before fermentation. Tubular heat exchangers enable:· Efficient heat removal using chilled water or glycol as a cooling medium.
· Prevention of contamination, thanks to separate fluid paths and sanitary design.
2. Heating Liquids for Mashing or Sparging
In the mashing process, water must be heated to precise temperatures to convert starches into fermentable sugars. Tubular heat exchangers provide:· Uniform heat transfer to achieve consistent mash temperatures.
· High efficiency, reducing energy consumption.
3. Temperature Control During Fermentation
Maintaining precise fermentation temperatures is critical for yeast performance. Tubular heat exchangers:· Enable controlled cooling using glycol systems.
· Help maintain consistent fermentation profiles.
4. Energy Recovery
Tubular heat exchangers can recover heat from hot waste streams and use it to preheat incoming water, improving the brewery’s energy efficiency.What is the Difference Between Tubular Heat Exchangers and Plate Heat Exchangers?
While both tubular and plate heat exchangers are used in beer brewing, they differ in design, application, and performance characteristics.Aspect | Tubular Heat Exchanger | Plate Heat Exchanger |
Design | Tubes inside a shell | Thin plates stacked together |
Hygiene | High; easy to clean and sanitize | High, but requires more cleaning effort |
Durability | Robust; handles high pressures and fouling | Less durable; more prone to leaks |
Applications | Best for viscous or particulate fluids | Ideal for low-viscosity fluids |
Maintenance | Simple; fewer gaskets | More gaskets require regular inspection |
Cost | Higher initial cost | Lower initial cost |
How to Design Tubular Heat Exchanger Capacity?
Designing the capacity of a tubular heat exchanger involves careful consideration of the brewing process’s thermal requirements, fluid properties, and operational constraints. Here’s a step-by-step guide:1. Determine Heat Load
The heat load is the amount of heat that needs to be transferred. It is calculated using:Q=m×Cp×ΔTQ = m \times C_p \times \Delta TQ=m×Cp×ΔT
Where:
· QQQ: Heat load (kW or BTU/hr)
· mmm: Mass flow rate of the fluid (kg/s or lb/hr)
· CpC_pCp: Specific heat capacity of the fluid (kJ/kg·K or BTU/lb·°F)
· ΔT\Delta TΔT: Temperature difference (°C or °F)
2. Assess Fluid Properties
Understanding the properties of the fluids involved, such as viscosity, density, and thermal conductivity, ensures accurate sizing and optimal performance.3. Define Flow Configuration
· Parallel Flow: Both fluids flow in the same direction.· Counterflow: Fluids flow in opposite directions, maximizing heat transfer efficiency.
· Crossflow: One fluid flows perpendicular to the other.
Counterflow configurations are most common in brewing for their efficiency.
4. Select Tube Dimensions and Material
· Tube diameter and length influence heat transfer surface area.· Stainless steel is the preferred material for its hygiene and corrosion resistance.
5. Calculate Heat Transfer Coefficient
The overall heat transfer coefficient combines the heat resistance of the tube walls and fluid films. It is calculated using:1U=1h1+Rwallk+1h2\frac{1}{U} = \frac{1}{h_1} + \frac{R_{wall}}{k} + \frac{1}{h_2}U1=h11+kRwall+h21
Where:
· UUU: Overall heat transfer coefficient
· h1,h2h_1, h_2h1,h2: Heat transfer coefficients of the fluids
· RwallR_{wall}Rwall: Thermal resistance of the tube wall
· kkk: Thermal conductivity of the tube material
6. Evaluate Pressure Drop
The design must minimize pressure drop to ensure smooth fluid flow without excessive energy loss.7. Sanitation and Maintenance Requirements
For breweries, hygienic design is essential. Ensure the exchanger is CIP (Clean-In-Place) compatible and easy to disassemble if needed.Tiantai’s Expertise in Tubular Heat Exchangers for Breweries
Tiantai Company specializes in providing breweries with high-quality, customized tubular heat exchangers designed for optimal performance in beer production. Here’s how Tiantai stands out:1. Tailored Solutions
· Designs adapted to the specific needs of each brewery.· Custom tube lengths, diameters, and materials for maximum efficiency.
2. Sanitary Standards
· Equipment built with stainless steel to ensure hygiene and durability.· Smooth interiors minimize fouling and simplify cleaning.
3. Energy Efficiency
· Integrated heat recovery systems reduce operational costs.· Counterflow designs maximize heat transfer efficiency.
4. Turnkey Services
· Complete support from initial design to installation and commissioning.· Training and after-sales service to ensure smooth operation.
Conclusion
Tubular heat exchangers play an essential role in modern beer brewing, offering precise temperature control, energy efficiency, and robust performance. While they may have a higher initial cost compared to plate heat exchangers, their durability, hygiene, and adaptability make them a superior choice for breweries prioritizing quality and efficiency.Tiantai Company provides breweries with cutting-edge tubular heat exchangers as part of their comprehensive beer brewing equipment lineup. With decades of experience and a commitment to customer satisfaction, Tiantai ensures your brewery is equipped for success.
For more information on Tiantai’s tubular heat exchangers and other brewing equipment, visit their website and explore how they can help you optimize your brewing process.
Contact Information:
Email: [email protected]
Contact Person: Emily Gong
Get In Touch