However, the rub here is that pot stills are not really the most efficient tools to use if production speed factors heavily into your planning. The main limitation is that a pot still can really only render an aggregate ABV of 35% to 45% alcohol from an 8% to 10% beer with a single distillation.
Furthermore, because of the pot still’s inherent inefficiency, the resulting distillate from a single distillation can be highly contaminated with high and low boiling-point constituents that can impart an unpleasant quality in the finished distillate. For this reason, most operators choose to run the distillate a second time to produce a more desirable finished product. Of course, this all adds up to the utilization of more resources to produce the most desirable pot-stilled finished product. Namely, more heating, more cooling and, especially, more man hours.
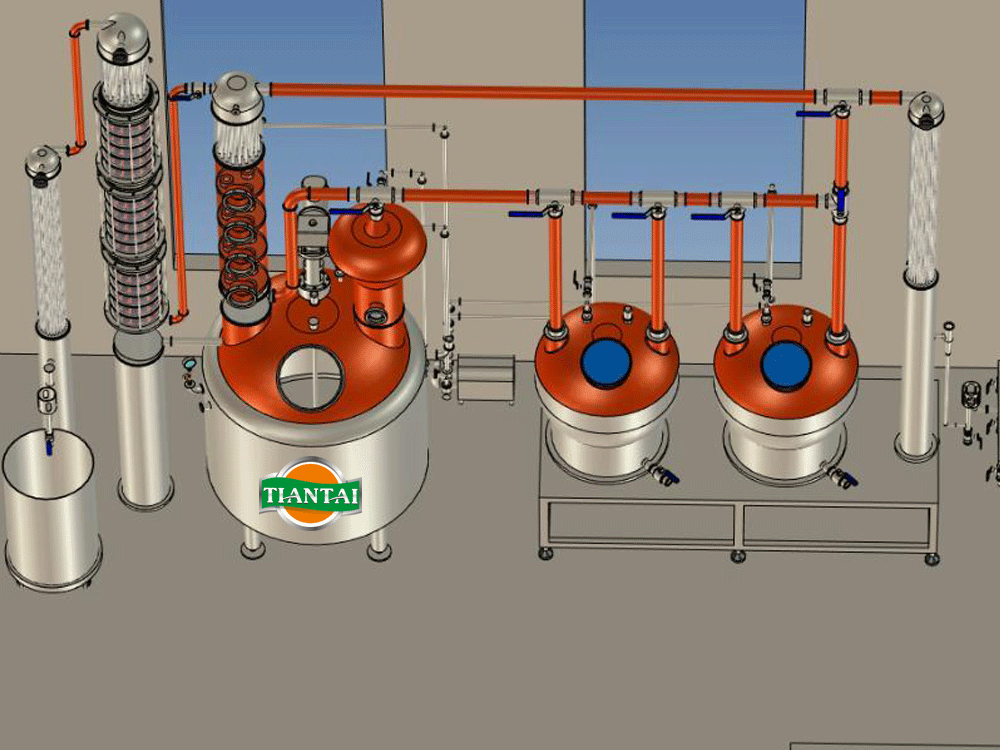
What Is a Thumper?
A thumper is essentially a parasitic kettle connected to the primary distilling kettle. The thumper gets heated with the heat already produced to feed the primary kettle. Evidently, the thumper gets its name from the sound it makes while in operation.
Thumper or No Thumper?
A thumper setup allows for a secondary distillation without having to run the distillate a second time. Based on the design parameters, the use of a parasitic kettle may require more BTUs to run than a single distilling kettle, but likely not as many BTUs when compared to running two completely separate distillations. In addition, since the thumper contains a measure of liquid to facilitate another phase-change cycle, there will be heat exchange occurring within the thumper that may reduce the amount of cooling capacity required to cool the finished distillate.
Again, these variables would be predicated upon the design and size of the parasitic kettle. The noteworthy savings, however, will be man hours needed to render a product that is more desirable for consumption.
The operator can choose to “charge” the thumper with water, alcohol, or even an additional flavoring component that may result in the formation of additional carboxylic acids that can add to the complexity of the finished spirit. Similarly, the operator can also add botanicals to the thumper for gin production. Doing so allows the operator to keep the larger, more time-consuming-to-clean, primary distilling kettle from being contaminated with botanical oils.
Enter the Double Thumper
In addition to a single thumper, a double thumper (or double retort) can be used. Like the single thumper, the double thumper further adds to the ABV enrichment of the finished product by stabilizing the ABV of the resulting distillate.
Perhaps the most widely known version of a double thumper (retort) system is the alcohol still used for making traditional Jamaican-style rum. In this application, one of the retorts is charged with low wines, and the other with high wines. The primary distilling kettle is charged with the rum beer. This process facilitates an additional boost in ABV as well as enhances the likelihood of desirable carboxylic acid formation, as previously mentioned. This is all meant to maintain a more stable ABV collection strength as well as to install more complexity into the finished product. You could say this type of arrangement adds more “rummyness” into the rum.
A More Flexible Double Thumper
The double thumper (retort) system takes this concept a bit further by providing additional features to allow the operator more flexibility during operation. In the still system, the vapor supply manifold (lyne arm) is equipped with three-way valves at each retort to give the operator the ability to bypass either or both retorts. This is helpful if the operator chooses to do a more basic stripping run or to send vapor to a completely separate distilling apparatus. In other words, the operator is not limited to only running the system solely as a double retort.
Each still retort is also typically equipped with dedicated heat input capability and a conventional column attachment feature. This allows the distiller to utilize either retort as a smaller, primary distilling kettle for smaller batches, if needed.
Other features can also be included. For example,we can create a custom piping solution that will allow for multiple product condensers, additional vapor infusion hardware, and even a rectifying column by controlling the vapor path with valves.
Below is a classic example of how multiple types of distillation tools can be incorporated together to make the most versatile distilling apparatus. The below system can be configured to run as a traditional pot still, single or double thumper, small column for bright clean mouth feel on flavored spirits, and finally a full rectifying column for more neutral spirits.
This system is also outfitted with a dedicated product condenser to reduce the need for cleaning on the rectifier side of the system. The valved manifold even allows the operator enough flexibility to simultaneously run the primary distilling kettle and the retorts independently, so that each kettle on the system can be used to produce a completely different finished product.
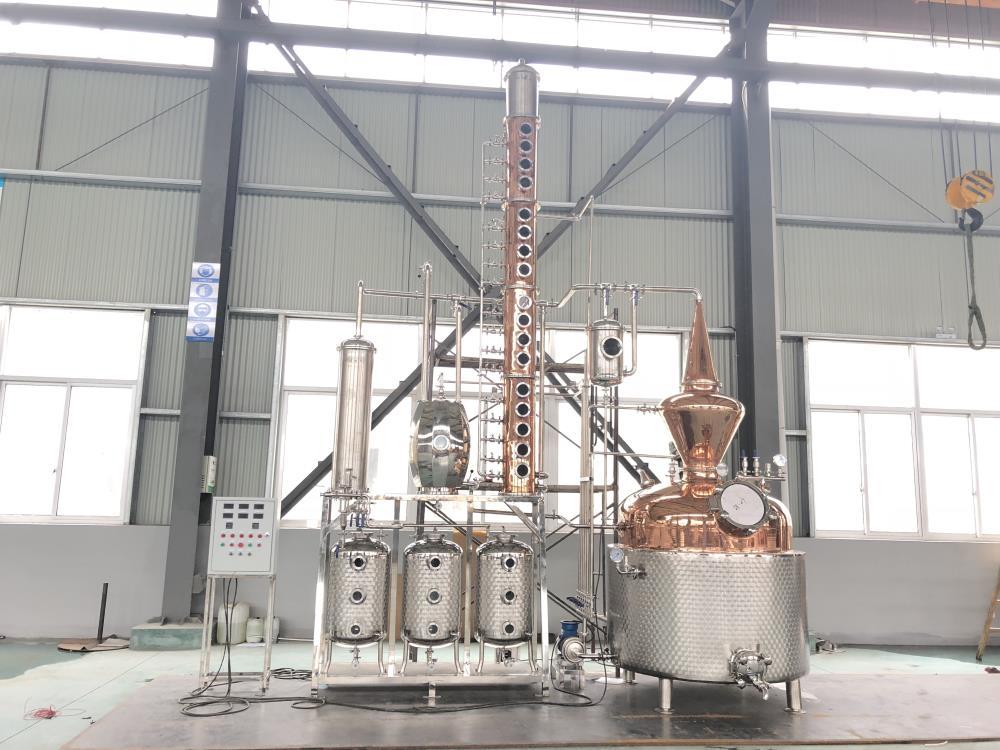
Edited By Daisy
[email protected]
Get In Touch