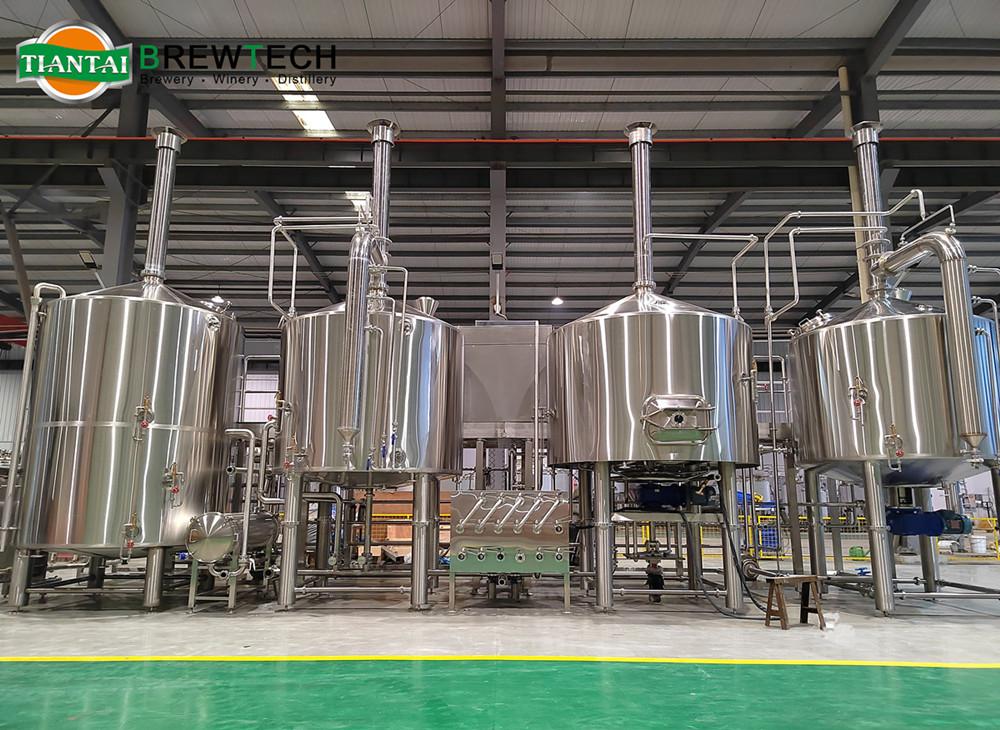
The hardware components of a PLC system may vary depending on the specific application but typically include a processor or CPU, power supply, input modules, output modules, and communication modules. The processor or CPU is the core of the PLC, executing all necessary computations and logical operations. The power supply provides electricity to the PLC, while the input and output modules connect the PLC to real-world devices such as sensors, valves, and motors. The communication module allows the PLC to communicate with other devices or systems.
PLC systems can be used to control various brewing processes, including temperature control during fermentation and maturation, filling and packaging, and process management. In most brewery or brewpub control systems, temperature sensors, pressure sensors, and other input devices are connected to the PLC input modules. The PLC program then uses this input data to control output modules connected to valves, pumps, and other control devices.

For example, during the fermentation process, the PLC can control the temperature of the fermentation tank by opening or closing cooling valves based on temperature sensor readings. The PLC can also monitor the pressure inside the fermentation tank and automatically adjust the pressure relief valve as needed. This automation helps ensure that the beer is produced consistently and meets the desired specifications.
Both PID and PLC controls are used in brewing control, but they have some key differences in terms of functionality, complexity, and cost.
PID (Proportional-Integral-Derivative) control is generally simpler and cheaper than PLC control. It is designed to regulate temperature and maintain consistency during the brewing process. Using feedback loops, it monitors temperature sensors and adjusts heating elements, pumps, and valves to keep the temperature stable within a narrow range.
On the other hand, PLC control panels are more complex and expensive. In addition to temperature regulation, they can control multiple processes, such as pump control, valve control, and automation of the brewing process. PLCs can also integrate with other systems, such as data logging, recipe management, and remote access.
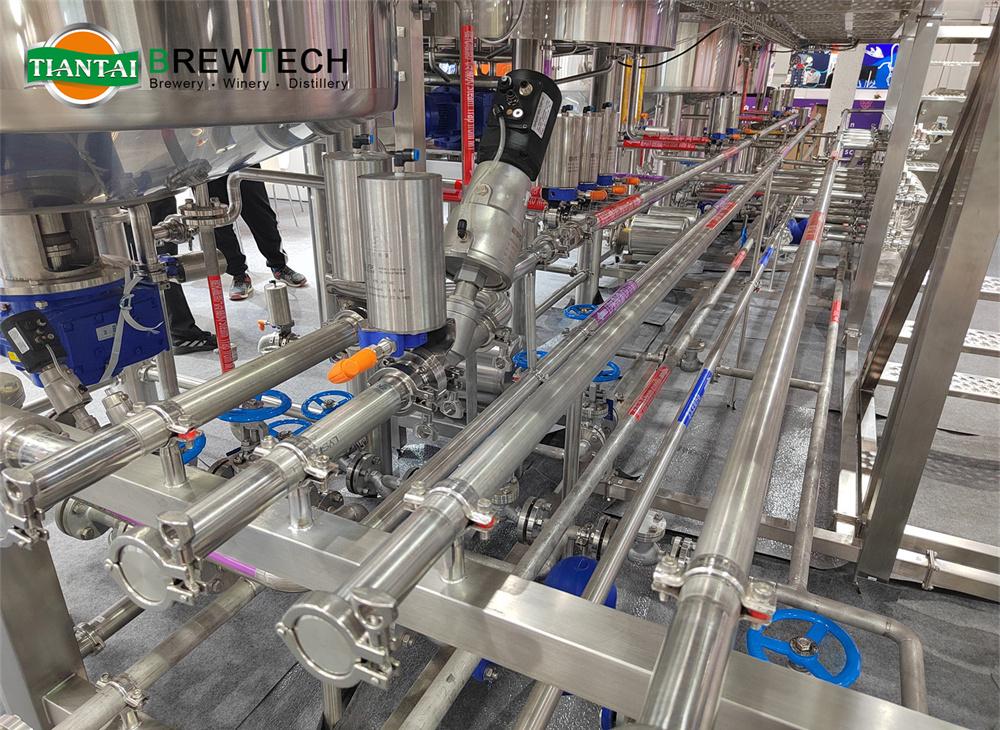
PID controls are usually easier to operate, featuring intuitive interfaces and fewer programming requirements. PLC control panels are more complex and require more technical expertise to operate and maintain.
For breweries with a high demand for automation and standardization, PLC control might be the best choice. It can automate many steps in the brewing process, freeing up employees to focus on other aspects of the operation and ensuring consistent beer quality. However, in smaller brewpubs or craft breweries, where brewing relies more on manual craftsmanship, PID control might be more suitable. It allows for precise temperature control and consistency while still enabling brewers to make adjustments based on their knowledge and experience.
Learn more how Tiantai beer equipment company to not only produce the best quality brewery equipment for flavor-rich beers, but also help them to optimize the configuration, maximize process uptime and reduce beer loss when they brewing, PLEASE DON’T HESITATE TO CONTACT WITH US!
Hubert
Email: [email protected]
Get In Touch